On définit généralement le jumeau numérique comme étant la représentation virtuelle d’un objet ou produit physique. Cette représentation virtuelle peut inclure des modèles de conception, de simulation ou autres qui évoluent au fil du temps, à mesure que le produit, processus ou objet physique représenté mûrit. En d’autres termes, le jumeau numérique fusionne le monde virtuel et le monde réel, brouillant les frontières entre les domaines de l’ingénierie et des processus.
Cette conception du jumeau numérique est toutefois trop limitée au regard des défis auxquels les entreprises font face aujourd’hui. La complexité s’accroît, les coûts augmentent et la nature de la main-d’œuvre dans les équipes d’ingénierie et de production évolue. Pour relever ces défis avec succès, il faut s’engager dans une numérisation à grande échelle et avoir une conception beaucoup plus large de ce qu’est le jumeau numérique et de ce qu’il peut faire.
Les solutions de demain s’appuieront sur un jumeau numérique complet englobant tous les modèles et données interdomaines, de la CAO mécanique et de l’IAO au code logiciel en passant par les nomenclatures, les nomenclatures de processus, etc.
Ce jumeau numérique complet possède les caractéristiques suivantes :
- Il offre une représentation virtuelle précise du produit (ou du flux de processus), qui correspond exactement à la forme physique, aux fonctions et au comportement du produit et de ses configurations.
- Tout au long du cycle de vie du produit et du processus, il permet de simuler, prévoir et optimiser le produit et le système de production utilisé pour le créer.
- Pendant toute la durée de vie du produit, il réinjecte dans les étapes de conception et de production du produit les données d’exploitation recueillies dans le monde réel, afin d’améliorer en permanence la qualité et l’efficience du produit et de répondre rapidement aux exigences des clients ou à l’évolution du marché.
Il continue d’évoluer et de mûrir en même temps que le produit, à mesure que les fonctionnalités de celui-ci sont affinées, que les simulations sont achevées, que les résultats des essais sont recueillis et que les modifications de conception sont mises en œuvre. Étant connecté à l’Internet des objets (IoT) et à des outils d’analyse de données hébergés dans le cloud, le jumeau numérique complet fait également partie d’un mécanisme de rétroaction en boucle fermée entre la conception du produit, le système de production et le produit sur le terrain. Il en résulte un système intégré qui permet de valider, comparer et optimiser le comportement des actifs physiques et du jumeau numérique complet.
Cela présente non seulement des avantages à court terme mais aussi des avantages durables, car la réutilisation de ces données peut contribuer à accélérer les évaluations de conception et les analyses de compromis, ce qui permet de prendre des décisions plus rapidement. En outre, le jumeau numérique complet permet aux entreprises de concevoir, fabriquer et optimiser leurs produits de nouvelle génération plus rapidement et pour un coût plus bas que jamais, avec moins de prototypes, moins d’essais et moins de déchets pendant la production. Il offre ainsi un avantage concurrentiel évident au regard des attentes croissantes des clients en matière de performances et d’intelligence fonctionnelle, tout en aidant à surmonter les problèmes liés à l’augmentation de la complexité, à l’évolution de la main-d’œuvre et à la nécessité de concevoir des produits respectueux de l’environnement.
Le jumeau numérique complet constitue l’interface entre le réel et le virtuel ; il relie le physique et le numérique et fournit la base matérielle des produits, processus et autres données résidant dans le monde virtuel. Sur cette base, plusieurs autres technologies-clés contribueront à renforcer la puissance du jumeau numérique complet, à accroître la richesse des données disponibles et même à inventer de nouvelles méthodes de collaboration et de travail.
Quelques tendances et technologies pour l’avenir
L’ingénierie des logiciels et des systèmes (SSE, pour software and systems engineering). La SSE est une méthodologie qui établit un processus de développement connectif permettant aux différents domaines d’ingénierie de concevoir ensemble les produits au lieu de travailler de manière isolée. Elle permet de créer une continuité numérique solide constituée de données de conception, de résultats d’essais, de simulations et d’autres artefacts du développement de produits, en veillant à ce que ces données soient accessibles au moment et à l’endroit où elles sont nécessaires. Comme les logiciels occupent une place sans cesse croissante dans les produits de tout type, la SSE va devenir indispensable pour gérer les données tout au long du cycle de développement des produits.
La convergence des technologies de l’information et des technologies opérationnelles (IT/OT). Cette convergence constitue une priorité majeure pour les écosystèmes de fabrication et de conception. Elle apportera une flexibilité et une visibilité accrues, permettant aux industriels de prendre des décisions en toute connaissance de cause grâce à la surveillance en temps réel des processus des usines. Elle permettra également aux responsables d’évaluer facilement l’impact commercial de la production, et elle soutiendra et encouragera la collaboration entre la planification, l’ordonnancement et l’exécution dans l’usine, conduisant ainsi à une meilleure efficience.
À mesure que de plus en plus de données seront générées et injectées dans l’écosystème de conception et de production, les entreprises auront besoin de méthodes permettant de gérer et analyser ces données pour en tirer des enseignements. L’intelligence artificielle (IA) sera essentielle pour augmenter la vitesse de traitement et le débit de données, et permettre ainsi de créer et évaluer plus vite de nouveaux produits et processus. Aujourd’hui, l’IA peut déjà aider à automatiser des tâches courantes, ce qui permet aux ingénieurs de consacrer plus de temps à la résolution des problèmes de conception. À l’avenir, elle pourra commencer à automatiser des tâches plus complexes et avoir un impact plus important sur la conception et l’optimisation des futurs produits.
Enfin, le métavers industriel (MI) continue de montrer son potentiel pour réinventer la façon dont les produits sont conçus, fabriqués et entretenus. En appliquant dans le métavers industriel la physique maîtrisée dans le jumeau numérique complet, nous pouvons créer un environnement partagé et immersif où l’apprentissage est plus rapide et plus intuitif, où les idées de conception sont plus faciles à comprendre et où de nouvelles idées peuvent être étudiées rapidement et en profondeur pour stimuler l’innovation de demain.
Chacune de ces technologies et tendances s’inscrit dans une dynamique plus large de transformation numérique. La maîtrise et la synthèse de ces technologies permettront aux entreprises de progresser dans leur parcours numérique, d’atteindre des niveaux de maturité plus élevés et de mettre en œuvre des outils puissants tels que la conception générative et l’optimisation en boucle fermée.
La complexité du développement des produits, de la fabrication et des processus d’entreprise va continuer de croître. Les entreprises qui choisissent de s’engager dans la voie de la transformation numérique seront en mesure de relever avec succès les défis qui se profilent à l’horizon et de prendre une longueur d’avance sur la concurrence.
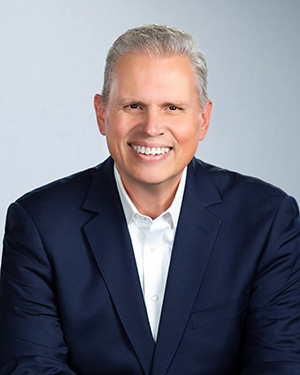
À propos de l’auteur :
Dale Tutt est le vice-président en charge de la stratégie industrielle chez Siemens Digital Industries Software. À ce titre, il dirige le développement de solutions de transformation numérique répondant aux besoins spécifiques des entreprises. Il a rejoint Siemens en 2019 en tant que vice-président chargé du secteur de l’aéronautique et de la défense. Avant cela, il a travaillé pour The Spaceship Company, une société sœur de Virgin Galactic, en tant que vice-président responsable de l’ingénierie et que vice-président responsable de la gestion des programmes, postes dans lesquels il a conduit le développement de vaisseaux destinés au tourisme spatial. C’est lui qui dirigeait l’équipe lors du vol spatial réussi qui a eu lieu en décembre 2018. Auparavant, Dale Tutt a travaillé pour Textron Aviation/Cessna Aircraft, où il a été responsable de programmes et de l’ingénierie. En tant qu’ingénieur en chef et directeur du programme Scorpion, il a dirigé l’équipe pluridisciplinaire dynamique qui a réussi – en seulement 23 mois – à concevoir, construire et faire voler le prototype de ce nouvel avion à réaction. Il a également travaillé en tant qu’ingénieur chez Bombardier Learjet et au sein de la division Space System de General Dynamics.